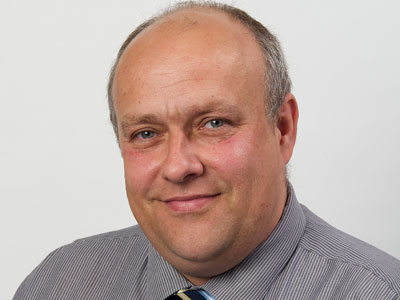
Author: Darren Bryant, Business Development & Applications Manager, Condair plc
Bad air day at the printers
We’ve all heard about, or worse experienced, those nightmare scenarios when paper seems to take on a mind of its own. It curls, moves, tears, sticks and creases, refusing any coaxing or cajoling from the long-suffering printer. The cost of these problems through lost production and poor quality can be very high, particularly when getting a good return on investment in presses and plant, and the high cost of paper demands maximum efficiency. But hold-ups due to paper problems can be resolved simply. Dry air is the cause; putting the moisture back into the air is the solution.
Paper is a natural material and is hygroscopic, which means that it is very susceptible to changes in relative humidity (RH). Low humidity environments are typically created between October and March in the UK, as heat generated by machinery and heaters dries the air. In the depths of winter, RH levels as low as 15-20% are not uncommon.
In these conditions, moisture is drawn from the exposed surfaces of stacks of paper and they shrink, but the centre of the paper still has its original moisture content. This causes “tight edges” and the paper begins to curl. As a result, the paper misfeeds and creasing occurs.
Changes in humidity can also cause the physical dimensions of the paper to change, albeit by tiny amounts, but enough to result in mis-registration of colours in multi-pass jobs. Any change in the dimensions of the paper, however small, between runs of a two or more colour process and the colours will not line up.
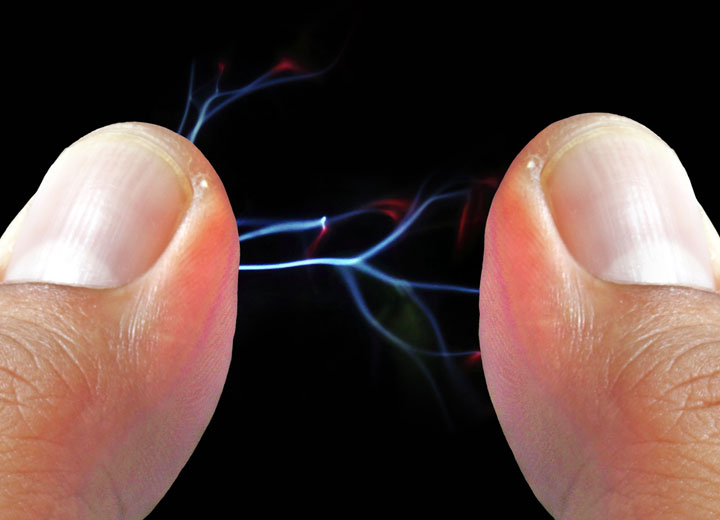
When the relative humidity drops below 40%RH, the build-up of static is enhanced...
Static electricity is another problem. When the relative humidity drops below the electrostatic threshold of 40%RH, the build-up of static is enhanced. This results in sheets of paper sticking and misfeeding, not lying flat on each other or stacking properly as they emerge from the other end of the press.
The problem is magnified when it comes to the giant web presses used by national and regional newspapers. During storage, and particularly in the lay-down and reel stand areas, the exposed edges of the reels dry. As the web runs at speed through the press, the dry edges are under tension compared with the centre. The slightest disruption of the edge will result in a ‘web break’, with the paper tearing right across its width, causing production downtime when deadlines are crucial.
So if low humidity is the culprit in all these situations, what can be done to counteract it? The answer, of course, is to fit humidifiers within the building.
Humidifiers have been around in the printing industry for many years. A widely used older type was the “spinning disc”, which hung from the ceiling or was mounted on the wall. This was basically a tank from which water was dripped onto a rapidly rotating disc, distributing it into the air. Unfortunately, a tank of water provides a good source of contamination and bacteria can breed readily if the water is stale, especially when paper dust and spray powder act as a nutrient. This resulted in print workers suffering from an illness known as humidifier fever, which produced flu-like symptoms such as a tight chest, headaches and sore eyes.
These days the technology has moved on and we use compressed air to project a fine spray of cold water through atomising nozzle jets. The water is first filtered and treated by ultra-violet light to ensure complete protection against any form of contamination. A typical system delivers about 100 litres of water an hour and, although every situation is different, a typical print work requires roughly 20 jets for every 1,000m2 of floor space in order to maintain correct levels of humidity. Modern systems are self-cleaning, drip-free and guarantee an even spread of humidity around the print shop. Alternatively, nozzles can be fitted into air conditioning ducts.
Steam humidifiers are another widely used option. They’re cheap to buy but high electrical and maintenance costs make this a poor option in whole life terms. An atomising system consumes less than a tenth of the energy of steam and payback compared to steam is typically well within a year.
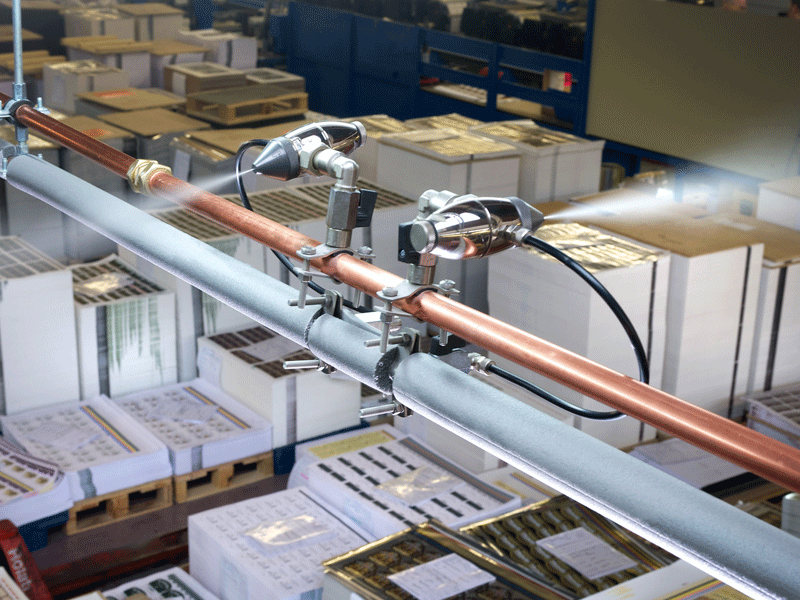
Normal printing conditions require a relative humidity of around 50-55%
The stories of low humidity levels causing havoc in the industry are legend, particularly amongst the national newspapers where any lost production time is a disaster. Some years ago, when the national newspapers moved from Fleet Street to Docklands, one printer experienced something like 54 web breaks in a single night. Although relative humidity had been considered in the new building, the systems installed were inadequate. Condair was called in the next day and installed a JetSpray humidifier system in the laydown area, and had it up and running by the same evening. That night, under exactly the same operating conditions, there were only four web breaks, demonstrating how crucial it is to have the humidity at the correct level.
Normal printing conditions require a relative humidity of around 50-55%, but some situations demand higher levels. Where water-based as opposed to oil-based inks are used, RH levels of around 60-65% are more appropriate. And with more and more people going over to water-based inks, it is becoming even more important to get the humidity at the correct level.
It’s not just a question of installing spray systems here, there and everywhere, though. There’s a large design element involved in the fitting of any humidification system. Apart from being capable of delivering the required amount of water for the size and shape of the building, it also has to be designed around existing fittings such as lighting, air conditioning, ductwork and all the other pieces of equipment that may be suspended from the ceiling. It’s important to use a professional company with real expertise in humidifier application, as every system must be customised to the client’s own building and each one is different.
It’s also important when designing a humidifier to check with the client that they’re not proposing any major changes to the configuration of the building in the near future, or adding something new which might impinge on the effectiveness of the system.
At Condair, we’ve installed equipment at over 120 sheet-fed and web print companies in the UK alone, and have built up a wealth of experience over the years. We’ve encountered all possible problems along the way and I think it’s fair to say that we’re more experienced than anybody else in the UK at applying humidifiers to print. The JetSpray system was originally conceived for the print industry, is virtually maintenance free and has extremely low running costs.
Low humidity is a seasonal problem. So when it turns cold use a hygrometer to check that the correct humidity levels are being maintained. If you have installed extra equipment since this time last year, it might generate enough extra heat to cause problems. If you’re unsure about your humidity levels, simply click here and ask us for a free on-site consultation.